PVC stands for polyvinyl chloride, a synthetic plastic polymer, also often referred to as vinyl, or poly vinyl. Flexible PVC containing platicizers (such as phtalates which pose a health hazard and leach into the environment) is unsuitable for use in windows due to its poor mechanical strength.
Traditional vinyl window framing is fabricated by melting solid unplasticized polyvinyl chloride (uPVC) and extruding it into a series of hollow channels, which are then cut and assembled together.
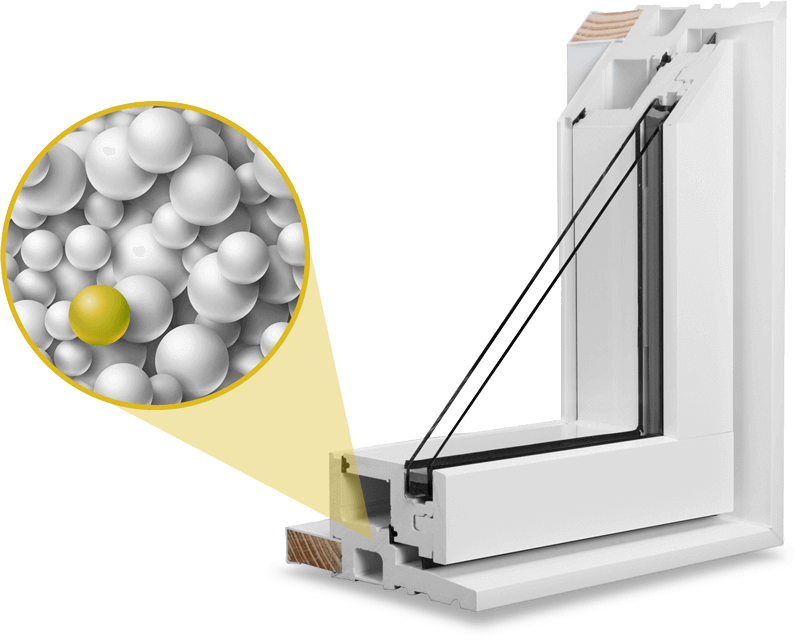
Microcellular polyvinyl chloride (mPVC) used in our RevoCell® windows is a material that has actually been in use in the construction industry for decades. The material is not new. What is new is the application of this technology to the manufacturing of windows.
mPVC is formed by a process called nucleation - which dissolves gas under high pressure into the liquefied uPVC as it's undergoing the extrusion process. This causes the uniform creation of billions of tiny bubbles which gives the material higher mechanical strength and lower thermal conductivity. Thus, the two major differences between uPVC and mPVC is that mPVC is much stronger and offers much better insulation (higher R-value).
The reason mPVC has taken so long to be developed as a material for use in window manufacturing is that the tolerances required for building window frames that hold insulated glass units are much higher than in other applications. Another challenge is that it is much more difficult to manufacture mPVC windows cost effectively, so most manufactures have chosen to stick with the existing uPVC window frame technology.
The Ottawa Citizen ran a recent article that explained how most window manufacturers will have to evolve to building their windows with this new mPVC technology or risk being left behind.